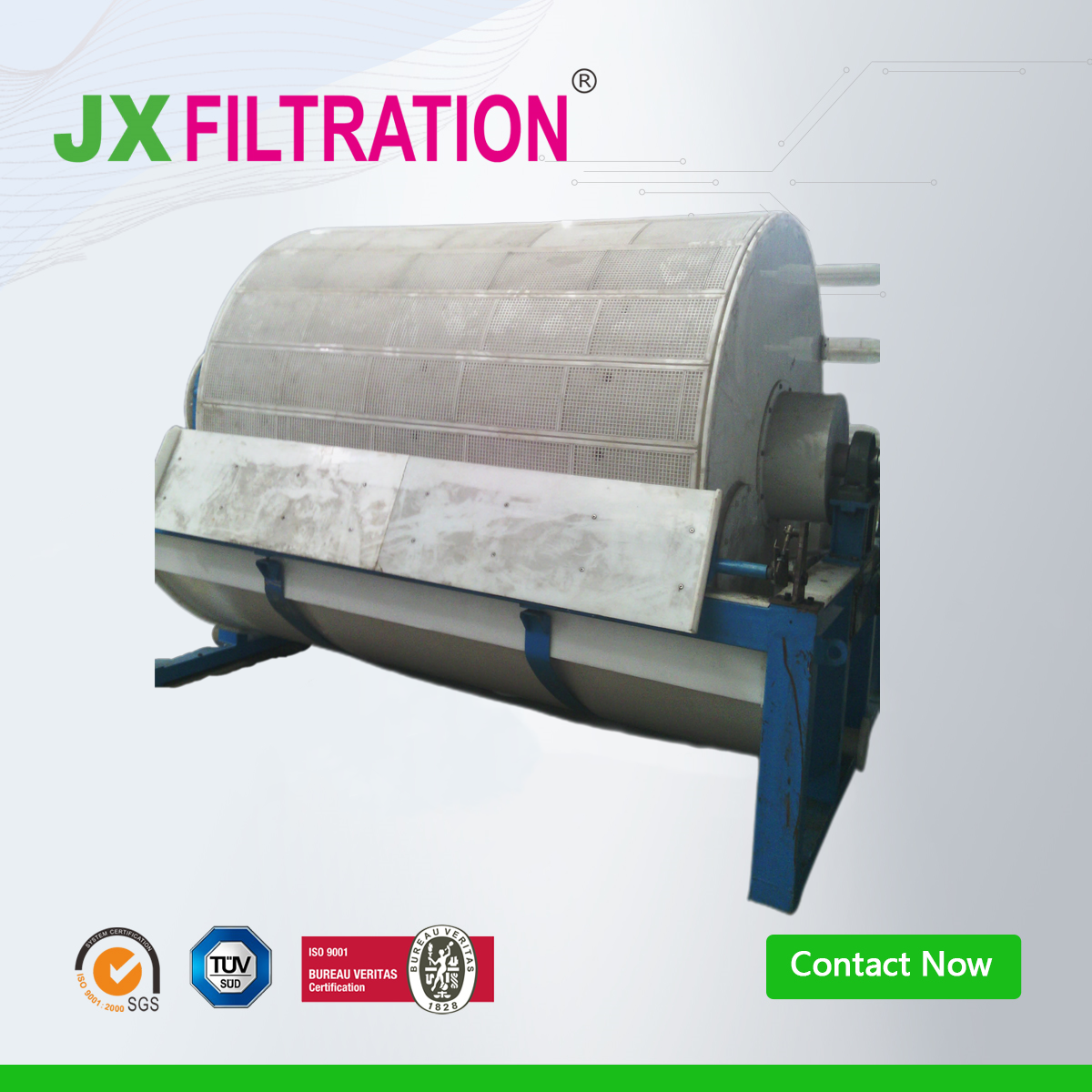
Application of Vacuum Drum Filter in Acrylic Fiber Factory
Background:
Acrylic fiber factories use sodium thiocyanate (NaSCN) solution as a solvent to produce acrylic fibers. The NaSCN solution is continuously recycled during the production process. The spinning device is formed after washing the tow with water, the dilute sodium thiocyanate solution and the ground wastewater containing NaSCN in the production are sent to the sodium thiocyanate recovery unit, and after purification treatment, they are evaporated and concentrated again. The evaporative condensate formed by the evaporation process is sent to the spinning device as washing water. The finished sodium thiocyanate (NaSCN) solution is sent to the polymerization unit as a solvent for preparing the dope for spinning. The ground wastewater returned from the spinning device and the cleaning liquid of the blade filter of the sodium thiocyanate recovery device contain a lot of oily dirt and suspended solid impurities. in sodium thiocyanate solution. Vacuum drum filter is one of the main impurity removal devices of sodium thiocyanate recovery device. Its operation not only affects the production of upstream and downstream processes, but also affects the consumption of filter aid diatomite to a large extent.
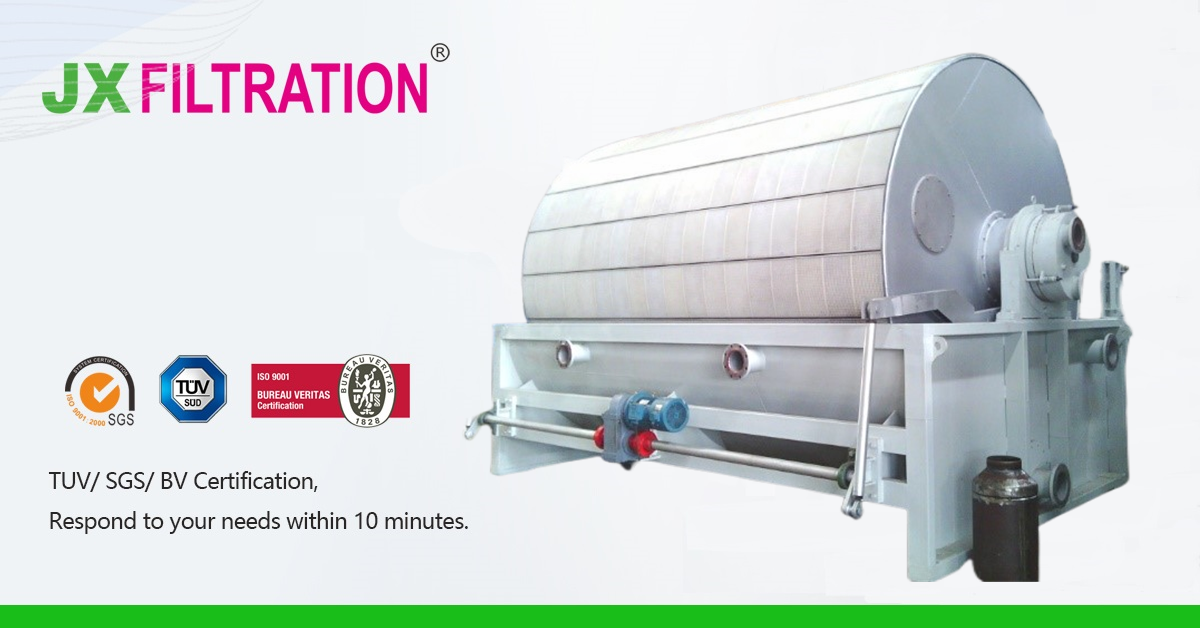
Application and working principle of vacuum drum filter:
At present, the vacuum drum filter is widely used in the industry, the maximum filter area is 200 m2, and the drum speed is mostly 0.1 to 10 min per revolution. The thickness of the filter residue can be adjusted by changing the speed of the drum speed. The absolute pressure of the vacuum formed during operation is 25-80 kPa, so the temperature of the filtered suspension should be lower than the vaporization temperature of the filtrate under the operating vacuum. The vacuum drum filter with which the filter residue can be washed is usually used to filter the suspension with high concentration of solid particles; the vacuum drum filter with pre-applied filter aid layer is used to clarify and filter the thin suspension, sodium thiocyanate This is what a recycling device is used for. The vacuum drum filter has a large processing capacity and is easy to operate. It is widely used in food, medicine, organic chemistry, wastewater treatment, grease and other industrial sectors. As a kind of continuous filter, the vacuum drum filter uses negative pressure (vacuum degree) as the driving force for filtration. The vacuum drum filter has a horizontal drum, the drum wall is perforated, and the drum surface is covered with a support plate and filter cloth to form a filter surface. The space under the filter surface is divided into several partitioned fan-shaped filter chambers. Each filter chamber has a conduit communicating with the distribution valve. Every time the drum rotates once, each filter chamber is connected to the vacuum system in turn through the distribution valve (some types are also connected to the compressed air system), and the operations such as filtration, slag washing, suction drying, slag unloading and filter media (filter cloth) regeneration are completed in sequence. On the entire filtering surface of the drum, the filtering area occupies about 1/3 of the circumference, the slag washing and drying area occupies 1/2, the slag discharge area occupies 1/6, and there is a transition section between each area. During filtration, the lower part of the drum is immersed in the suspension and rotated slowly. The filter chamber submerged in the suspension is communicated with the vacuum system, the filtrate is sucked out of the filter, and the solid particles are adsorbed on the filter surface to form a filter residue. After the filter chamber rotates with the drum to leave the suspension, it continues to absorb the saturated liquid in the filter residue. When it is necessary to remove the filtrate remaining in the filter residue, washing water can be sprayed when the filter chamber rotates to the upper part of the drum. At this time, the filter chamber is connected to another vacuum system, and the washing water permeates the filter residue layer to replace the filtrate remaining between the particles. The filtrate is sucked into the filter chamber and discharged separately, then the filter residue that has been sucked is removed, and the filter residue is scraped off by a scraper (some types of vacuum drum filter filter chamber is connected to the compressed air system, and the filter cloth is blown back to loosen the filter residue, and then scrape off the filter residue with a knife. The compressed air continues to blow back the filter cloth, which can unclog the pores and regenerate them)
Any Requirements, Contact Us Now!
Nina
Email/Teams:nina@filtrationchina.com
Mobile/Whatsapp/Wechat: +86 17269571060
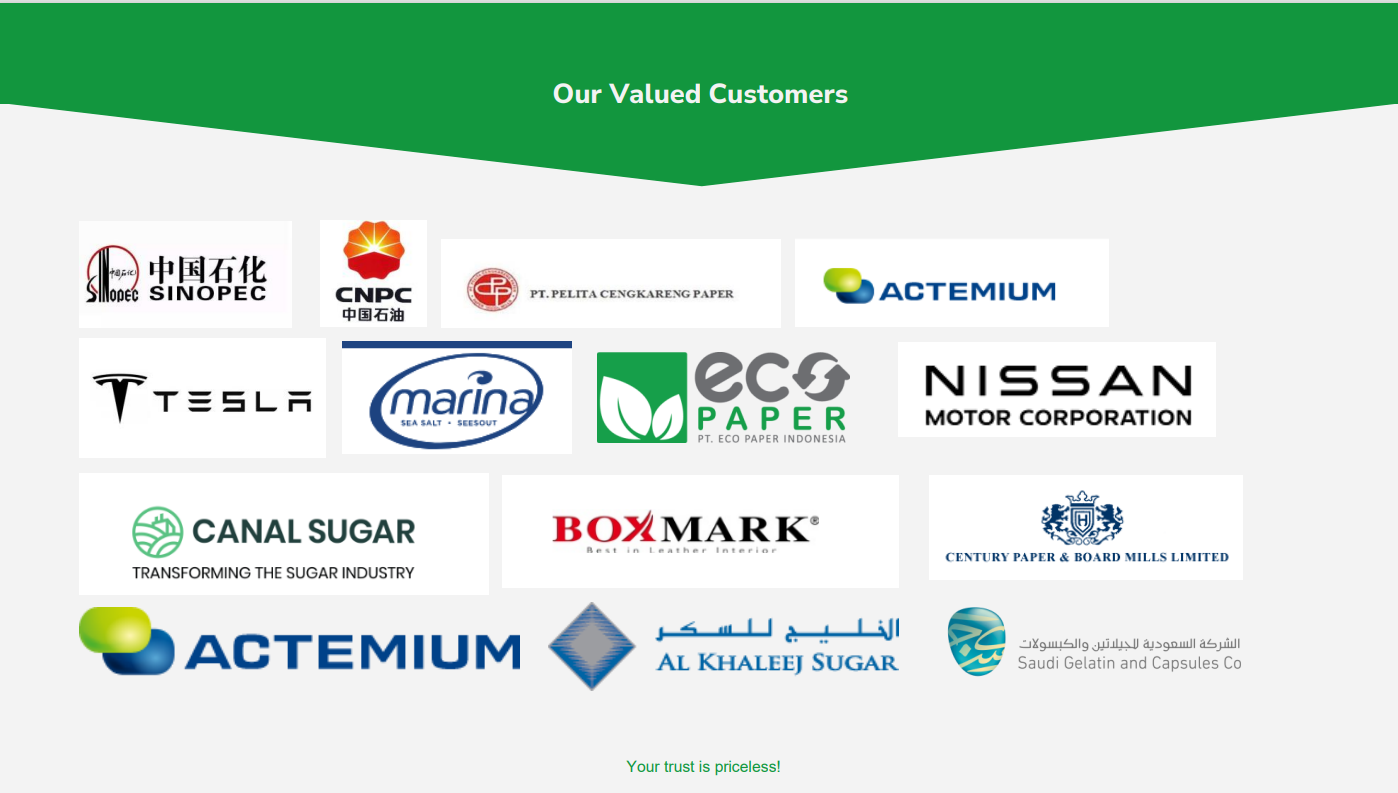