
Working Principle of Rotary Drum Screen
Working Principle:
1. The drum wall of the rotary drum screen is a horizontal opening, and the drum surface is covered with support plates and filter cloth to form a filter surface. The space below the filter is divided into individual fan-shaped filters. The piping and distribution valve are in the filter chamber. Every revolution, the filter chamber is connected to the filter (mud) vacuum system and mud cleaning in turn through the distribution valve. Vacuum drying system for filtration, mud cleaning, drying, slagging and filter media (filter cloth).
2. In the entire filtering surface of the filter cartridge, the filter layer area accounts for about 1/3 of the perimeter, the mud washing and drying area accounts for about 2/2, and the mud unloading area accounts for about 1/6. There are transition sections between each partition. After filtration, immerse the lower part of the drum in the suspension and rotate slowly. The filter chamber where the sediment is in suspension is connected to a vacuum system, the filtrate is sucked into the filter, and the solid particles are adsorbed on the filter surface to form filter mud. After the filter cavity rotates away from the suspension, it continues to absorb the liquid in the filter residue.
3. When the residual filtrate in the filter residue needs to be removed, the washing water can be sprayed when the filter chamber is transferred to the upper part of the drum. At this time, the filter chamber is connected to another vacuum system, and the washing water passes through the filter residue layer to replace the remaining filtrate. The filtrate is discharged separately through the filter chamber, and then the dry filter mud is removed.
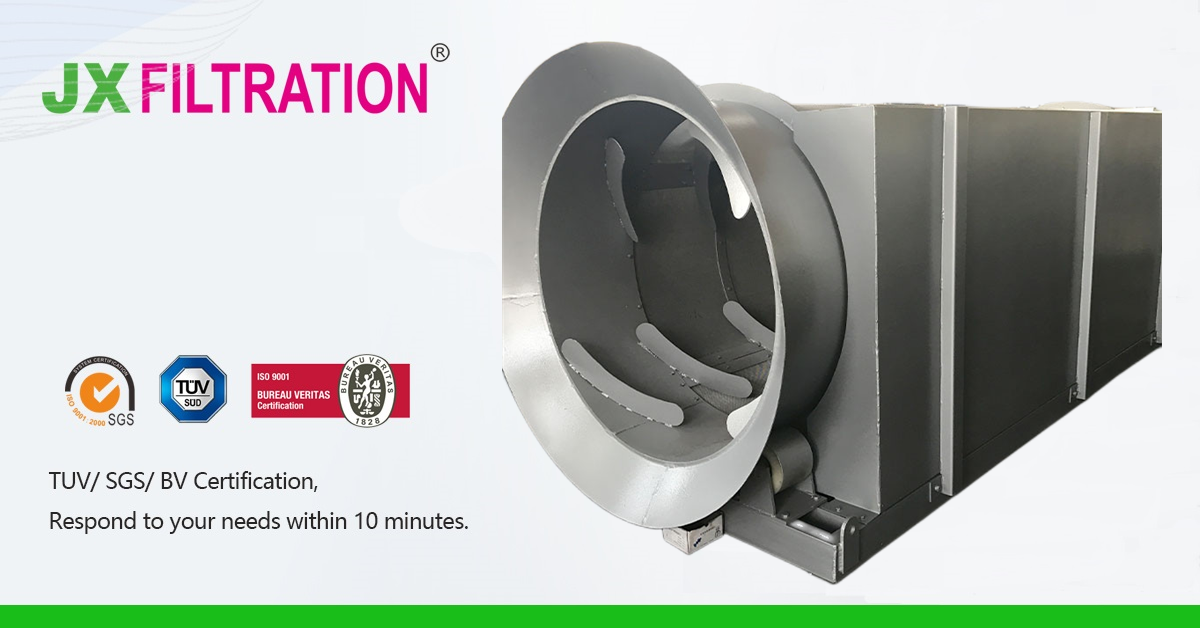
Maintenance:
1. Fix the bolts of the fixing parts once a year. Lubricating oil workers check the oil supply of the centralized lubricating pump every three days. Timely adjust the distance between the discharge roller mud scraping roller and the drum, so that the discharge roller can fully discharge.
2. Clean up the mud accumulated on the fender under the unloading roller in time. The filter should be repaired or replaced in time during use. When installing the filter cloth, be careful not to damage the cloth surface and bead groove. Every time you change the fabric, remove any mud buildup or scarring from the grooves.
3. When changing the cloth, the grid plate must be cleaned of scabs on the screen holes to make the holes unblocked. When the screen is deformed, it should be replaced in time. Be careful not to damage the filter cloth and sieve plate during equipment maintenance. Timely adjust the gap between the distribution head bridge plate and the valve body to ensure vacuum and leakage.
4. Open the drum hole every three months to check the inside of the drum. If oil leakage is found, it should be repaired in time and the accumulated material in the oil cylinder should be removed.
Any Requirements, Contact Us Now!
Nina
Email/Teams:nina@filtrationchina.com
Mobile/Whatsapp/Wechat: +86 17269571060
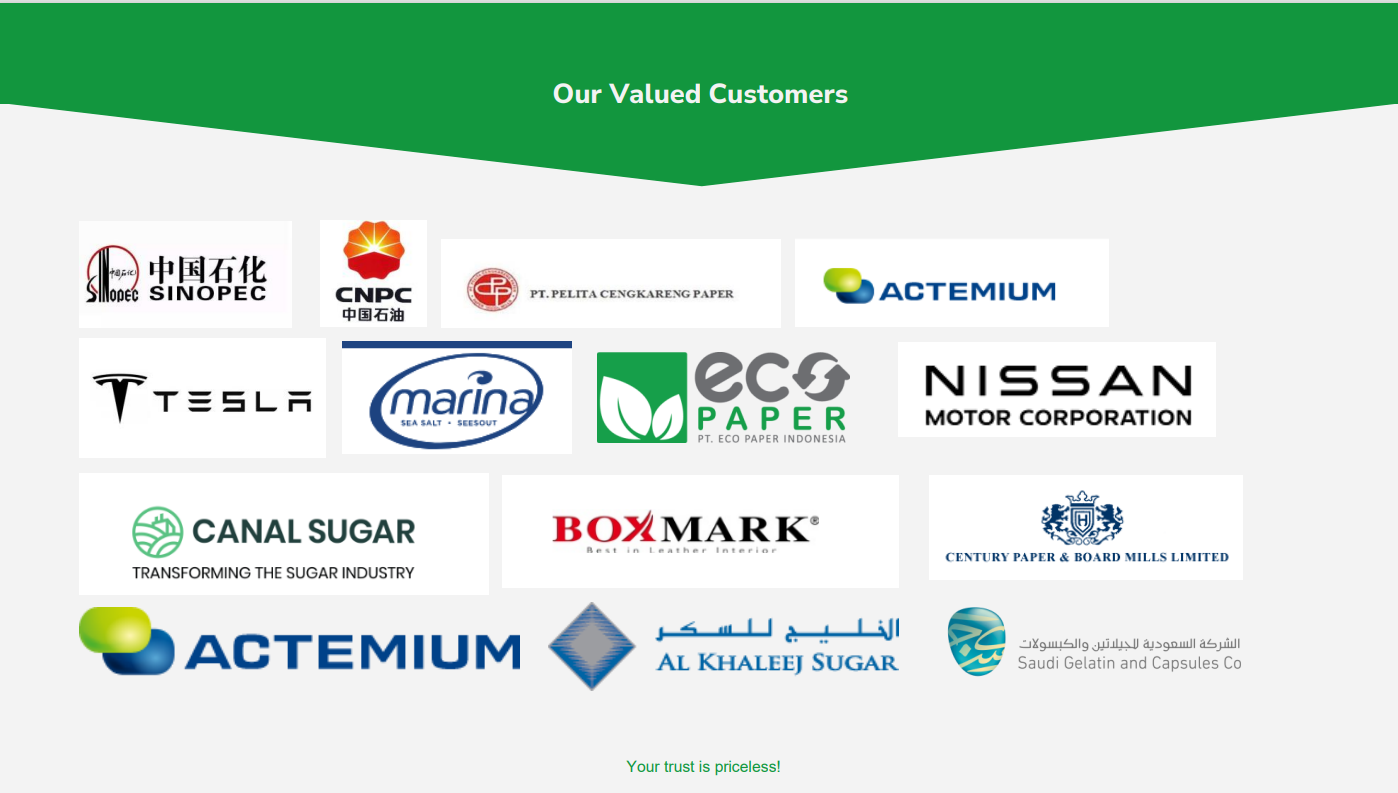